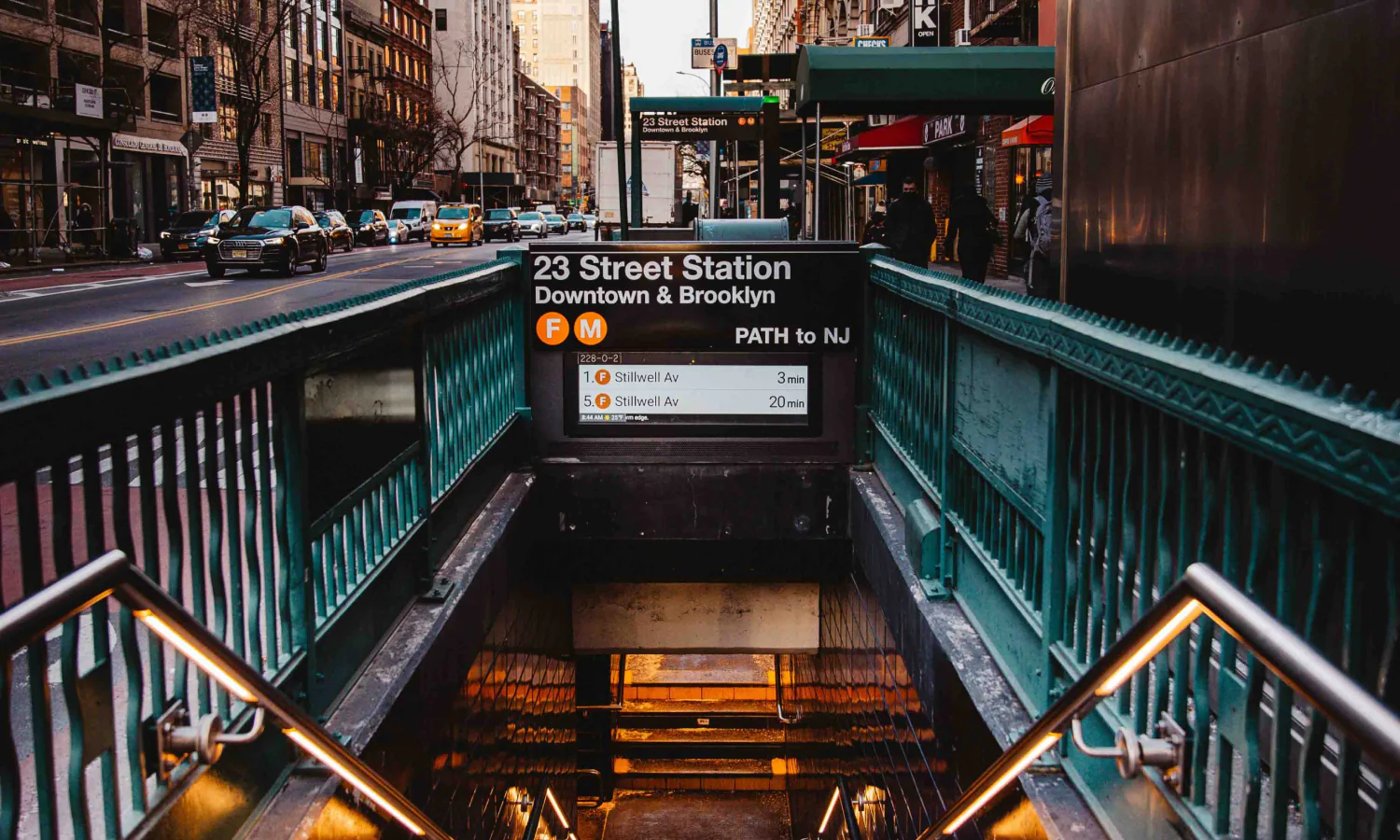
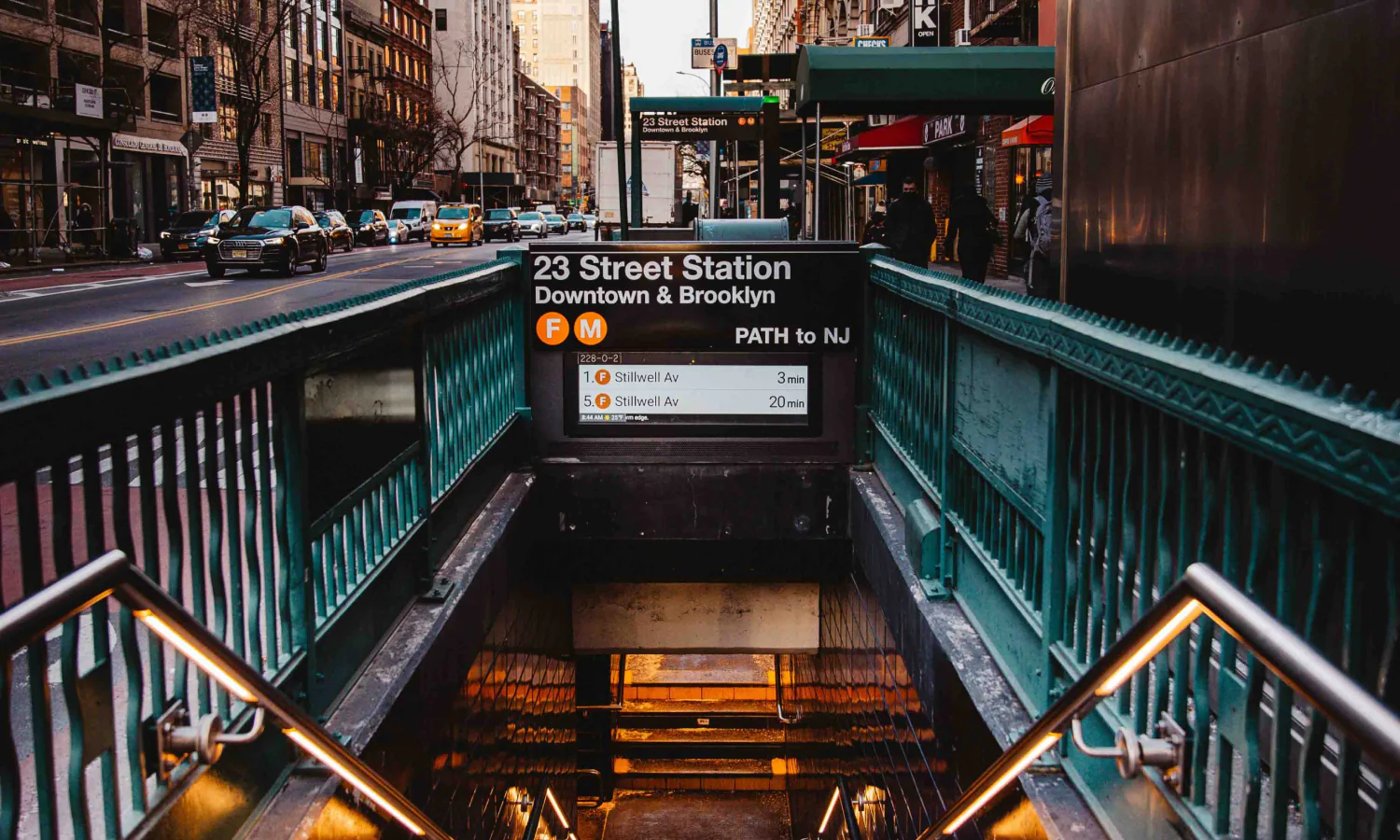
يكلفك الهدر المال وكذلك يفعل بزبائنِك وإذا ما كان سيتسبب بأن يدفع زبائنُك المزيد من المال فقد يبحثون عن بديلٍ لك. فالقدرة على المنافسة تحتاج أيضاً إلى كثيرٍ من المرونة لذلك يجب عليك أن تكون قادراً على تلبية الطلبات المتغيرة لزبائنك بسرعةٍ وكفاءة والتكيُّف مع بيئة العمل التي تتغير بشكلٍ سريع.
إذاً فكيف سيكون في إمكانك أن تقلل من الهدر وتؤدي الأعمال بمزيدٍ من الكفاءة؟ وكيف سيكون في إمكانك أن تواكب الطلبات المُتغيرة للزبائن؟
يُعَدُّ التصنيع الخالي من الهدر والذي ذُكِرَ أوَّل مرة في العام 1990 في كتاب “جيس ووماك” (James Womack) الذي يحمل عنوان “الآلة التي غيَّرت العالم” (The Machine That Changed the World) إحدى النظريات التي يمكن أن تساعدك على تبسيط بيئة عملك وتنظيمها بحيث تستطيع التقليل من الهدر والحفاظ على قدرة موظفيك ومعداتك وفضاء عملك على الاستجابة لما هو ضروري في الوقت الراهن.
نصيحة:
مثلما يمكن تطبيق مفهوم “التصنيع الخالي من الهدر” في المكاتب وبيئات العمل الأخرى يمكن تطبيقه أيضاً في منشآت التصنيع. فمن المفيد ربط كلماتٍ مثل “المخزون” و”الزبائن” و”الإنتاج” بأي شيءٍ تتعامل معه – سواءٌ كان بياناتٍ أم وثائق أم معرفةً أم خدمات إلخ.
لقد كان “هنري فورد” (Henry Ford) أحد أوائل الأشخاص الذين طوَّرا الأفكار التي تقف خلف فلسفة “التصنيع الخالي من الهدر”. فقد استخدم فكرة ما يُعرَف بـ “التدفق المستمر” (continuous flow) على خط تجميع سيارة الفورد “موديل تي” حيث فرض “فورد” معايير إنتاج شديدة الصرامة ممَّا أدى إلى تناسق مراحل العملية بعضها مع بعضها الآخر بشكلٍ مثالي وأدَّى في النتيجة إلى تضاؤل الهدر.
ولكنَّ عملية “فورد” لم تكن مرنة فقد أنتج خط التجميع لديه الشيء نفسه مراراً وتكراراً ولم يكن من السهولة بمكان أن تتيح العملية أيَّة تعديلاتٍ أو تغييرات على المنتج النهائي – فخط تجميع “موديل تي” لم ينتِج سوى “الموديل تي”. لقد كانت العملية أيضاً عملية “دفع” أي أنَّ فورد هو من يحدد مستوى الإنتاج ويدفع به نحو الزبائن بدلاً من أن تكون عملية “سحب” يقودها الزبائن و”يسحبون” من خلالها المنتج الذي يلبِّي طلبهم. فأدى ذلك إلى تخزين كمية ضخمة من السيارات التي لم تجد طريقها نحو البيع ممَّا نتج عنه في النهاية الكثير من الأموال المهدورة.
بدأ مُصنِّعون آخرون باستخدام أفكار “فورد” ولكنَّ العديدين منهم أدركوا أنَّ ثمَّة مشكلةً تتمثَّل في افتقار نظامه إلى المرونة. فطوَّر بعد ذلك “تاييتشي أونو” من شركة تويوتا نظام إنتاج تويوتا الذي استخدم لزيادة الكفاءة طرائق التصنيع المُسماة “الإنتاج المُبرمَج” (Just In Time). ولقد استخدمت تويوتا هذه العملية بشكلٍ ناجح كما ذكَر “ووماك” في كتابه وبرزت نتيجةً لذلك بوصفها واحدة من أكثر شركات التصنيع تحقيقاً للربح في العالم.
يعتمد منهج “التصنيع الخالي من الهدر” على إيجاد الكفاءات والتخلص من الخطوات المُسبِّبة للهدر والتي لا تضيف أية قيمة إلى المنتج النهائي. ومع “التصنيع الخالي من الهدر” ليس ثمَّة حاجة إلى تخفيض الجودة – فالتخلص من الخطوات هو نتيجة لإيجاد طرائق أفضل وأكثر كفاءة لإنجاز المهام نفسها.
لإيجاد الكفاءات يتوخى “التصنيع الخالي من الهدر” منهجاً يركز على قيم الزبائن ويجيب عن السؤال الآتي: “ما الشيء الذي يجعل الزبون راغباً في دفع النقود؟”. فالزبائن يريدون القيمة ولن يدفعوا إلَّا في حال تمكَّنت من تلبية احتياجاتهم. فهُم لا يمكن أن يدفعوا مقابل العيوب الموجودة في المنتَج أو مقابل التكلفة الإضافة المُترتِبة على تخزين كميات كبيرة منه. بمعنى آخر هم لا يمكن أن يدفعوا نتيجةً للهدر الذي تُعَدُّ أنت مسؤولاً عنه.
الهدر هو أي شيءٍ لا يضيف أية قيمة إلى المنتج النهائي وثمَّة ثمانية أصناف منه يجب عليك أن تراقبها:
ملاحظة:
ذُكِرَت المصادر السبعة الأولى للهدر في الأصل في “نظام إنتاج تويوتا” وأُطلق عليها اسم “مودا” (muda) وهي كلمة يابانية تعني الهدر. ويُضاف غالباً إلى “التصنيع الخالي من الهدر” الصنف الثامن والذي هو “القوة العاملة”.
يمنح “التصنيع الخالي من الهدر” الأولوية للتحسين البسيط والصغير والمستمر كتغيير موقع أداةٍ ما أو تقريب محطتَي عمل إحداهما من الأخرى. وعندما تتم إضافة بعض هذه التحسينات الصغيرة إلى بعضها الآخر فإنَّها يمكن أن تؤدي إلى مستويات أعلى من الكفاءة عبر النظام بأكمله (انتبه إلى أنَّ هذا التركيز على التحسينات الصغيرة لا يعني أنَّه ليس في استطاعتك إجراء تحسينات أكبر إذا كانت ضرورية).
ملاحظة:
على الرغم من أنَّ الهدف هو التخلص من أكبر قدرٍ من الهدر من خلال تنقيح عملياتك بشكلٍ مستمر إلَّا أنَّك على الأرجح لن تستطيع التخلص من الهدر بشكلٍ كامل.
ثمَّة في هذه العملية ثلاث مراحل أساسية:
وفقاً لفلسفة “التصنيع الخالي من الهدر” فإنَّ الهدر موجودٌ دائماً ومهما بلغت جودة عمليتك فإنَّها لا يمكن أن تسيطر على الهدر بشكلٍ كامل. ولكن فلسفة “التصنيع الخالي من الهدر” تعني الالتزام بالتحسين الدائم وهو ما يُطلَق عليه اسم “كايزن” (Kaizen) وهي كلمة يابانية تعني التغيير نحو الأفضل.
تُعَدُّ أداة “تخطيط تدفق القيمة” (Value Stream Map) إحدى الأدوات الأساسية المُستخدمة لإيجاد مواضع الهدر فهي تُظهر كيفية سير المواد والعمليات عبر منظمتك حتى تقديم المنتج أو الخدمة إلى زبائنك. فهي تنظر إلى مدى ترابط الإجراءات والإدارات وتسلط الضوء على الهدر. وعندما تحلل “تخطيط تدفق القيمة” سترى أيُّ العمليات تضيف القيمة وأيُّها لا تقوم بذلك. يمكنك بعد ذلك وضع مخططٍ مستقبلي لتدفق القيمة يتضمن أقل عددٍ ممكن من الأنشطة التي لا تضيف أي قيمة إلى المنتج أو الخدمة.
ابحث عن السبب الذي يقف خلف كل واحدة من عمليات الهدر التي حددتها في المرحلة الأولى باستخدام “تحليل السبب الجذري”. فإذا كان ثمَّة آلةٌ تتعطل بشكلٍ مستمر فقد تظن أنَّ المشكلة ميكانيكية فتقرر شراء آلةٍ جديدة ولكن تحليل السبب الجذري قد يُظهِر لك أنَّ السبب الحقيقي هو ضعف مستوى التدريب لدى العمَّال المسؤولين عن تشغيل الآلة والذين لا يستخدمونها بالشكل المناسب. ومن بين الأدوات الفعالة الأخرى لإيجاد السبب الجذري “العصف الذهني”.
باستخدام إحدى العمليات الملائمة لحل المشكلة حدد ما يجب عليك القيام به لحل المشكلة وتحقيق قدرٍ أكبر من الكفاءة.
بعد أن حددت العمليات التي تسبب الهدر باستخدام المراحل الثلاث الأساسية المذكورة أعلاه تستطيع تطبيق الأدوات الآتية لمساعدتك على الحد من الهدر بشكلٍ أكبر:
(إحدى الطرائق الأساسية للقيام بذلك في عملية التصنيع هي التي تُطبَّق باستخدام أداة “كانبان” المُشار إليها أدناه).
نصيحة:
تقدم هذه التقنيات حلولاً مُثْبَتة للتخلص من الهدر في منظمتك ولكن تذكر أولاً أن تطبق المراحل الثلاث لعملية ” التصنيع الخالي من الهدر وأن تتعامل مع أية مشاكل تظهر أمامك.
النقاط الرئيسة:
يركز التصنيع الخالي من الهدر الاهتمام على استغلال عملياتك والتخلص من الهدر فهذا يساعدك على خفض التكاليف وتقديم ما يريده الزبائن وما يرغبون في دفع المال مقابله. ستتمتع مع فلسفة “التصنيع الخالي من الهدر” بالفائدة التي ستجنيها من التحسن المستمر لذا بدلاً من القيام بتغييرات سريعة وغير منتظمة تُعَدُّ مُدمِّرةً لفضاء العمل يمكنك القيام بتغييرات صغيرة ومنتظمة يمكن للأشخاص الذين يتعاملون مع العمليات والمعدات والمواد المضي بها قُدُماً. إذْ يُعَدُّ هذا النهج المنظَّم والبسيط فعالاً للغاية في جميع أنواع الأعمال وبالإضافة إلى ذلك فإنَّ العملية الخالية من الهدر هي عملية أكثر استدامة.
المصدر